The Rise of Precision Plastic Injection Molding in Modern Business
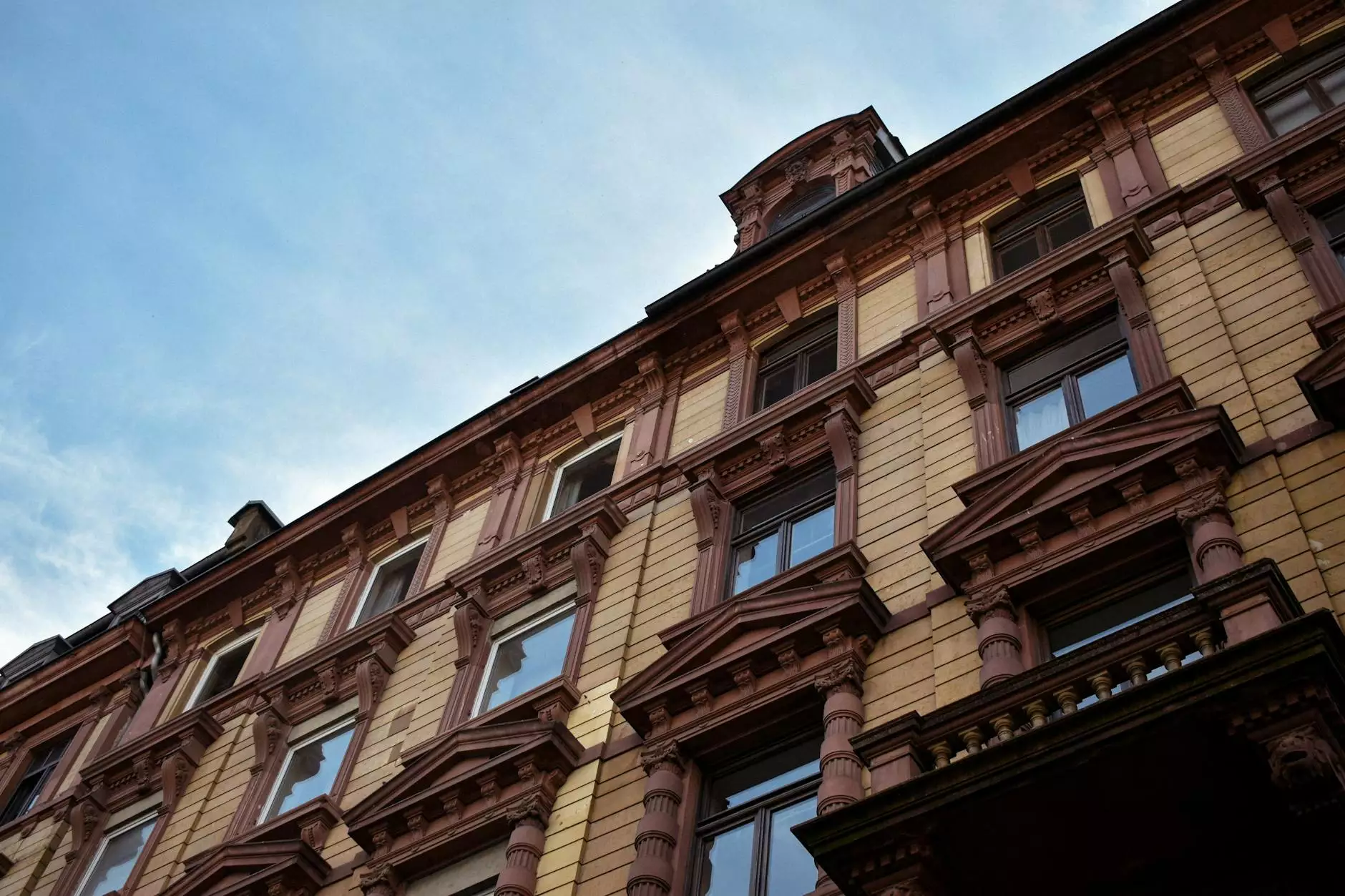
In today's rapidly evolving industrial landscape, one technology stands out for its remarkable efficiency and versatility: precision plastic injection molding. This manufacturing process is pivotal for creating complex plastic components that meet stringent industry standards. From automotive parts to consumer goods, the applications of precision plastic injection are vast and varied, making it a cornerstone of modern production techniques.
Understanding Precision Plastic Injection Molding
Precision plastic injection molding is a manufacturing process that involves injecting molten plastic into a mold to create parts with high precision and accuracy. The process begins with the selection of plastic materials that can be melted and injected into a specific mold. Once the material is heated and liquefied, it is forced into the mold under high pressure, where it cools and solidifies into the desired shape.
The Importance of Precision in Manufacturing
Precision is crucial in manufacturing, especially when creating components that require tight tolerances and intricate designs. The precision plastic injection technique allows manufacturers to produce parts that not only meet exact specifications but also function reliably in their intended applications. This capability is especially important in industries such as:
- Automotive: Components like dashboards, panels, and housing require precision to ensure compatibility and safety.
- Medical: Devices and components such as syringes, casings for electronic instruments, and surgical tools must adhere to stringent regulatory standards.
- Consumer Electronics: The production of lightweight yet durable casings for smartphones and tablets demands high accuracy.
- Aerospace: Critical components used in aircraft manufacturing must exhibit extreme precision to ensure safety and performance.
Benefits of Precision Plastic Injection Molding
Choosing precision plastic injection molding offers several advantages that are driving its adoption across various industries:
- High Efficiency: The speed of the injection molding process allows for rapid production rates, significantly reducing manufacturing times.
- Cost-Effectiveness: Although the initial mold-making process can be expensive, the ability to produce large quantities of high-quality parts quickly lowers the cost per unit.
- Design Flexibility: Advanced molding techniques allow for complex geometries that were previously impossible or too costly to produce.
- Material Versatility: A wide variety of thermoplastics and thermosetting plastics can be used, accommodating various performance requirements.
- Consistency and Quality: The automated nature of the process reduces the likelihood of human error, ensuring uniform quality across all produced parts.
Applications of Precision Plastic Injection Molding
The applications of precision plastic injection molding are virtually limitless. Here are some notable examples:
1. Automotive Industry
As one of the largest adopters of precision plastic injection molding, the automotive sector relies on this technology for:
- Interior and exterior trim parts
- Lightweight housings and brackets
- Fuel systems and components
The use of precision molded plastic components helps reduce vehicle weight and enhance fuel efficiency while maintaining durability.
2. Medical Devices
In the medical field, where safety and reliability are paramount, precision molding is employed for:
- Disposable syringes and catheters
- Surgical instruments and trays
- Patient monitoring devices
The stringent quality control measures associated with precision plastic injection are critical in meeting the regulations set forth by health authorities.
3. Electronics
Consumer electronics benefit from the advantages of precision plastic injection through:
- Lightweight and durable casings
- Custom connection housings
- Complex internal components that enhance performance
The ability to produce intricate designs leads to innovative products that capture consumer interest.
The Process of Precision Plastic Injection Molding
Understanding the precision plastic injection process involves several critical steps:
Step 1: Designing the Mold
The process begins with a detailed design of the mold. This is a crucial step that requires advanced software and collaboration between engineers and designers to ensure all tolerances and geometric specifications are met.
Step 2: Material Selection
Choosing the right material is vital to the success of the molding process. Factors such as strength, flexibility, and thermal stability influence this choice, given the application's requirements.
Step 3: Heating the Material
The selected plastic is heated until it reaches a molten state. The temperature and duration of the heating process are carefully controlled to prevent degradation of material properties.
Step 4: Injection
The molten plastic is injected into the mold at high pressures. This step must be executed with precision to ensure complete filling of the mold and eliminate defects such as air bubbles or incomplete sections.
Step 5: Cooling
Once injected, the material cools and solidifies. The cooling time can vary based on the complexity and thickness of the part being produced.
Step 6: Ejection
After cooling, the molded part is ejected from the mold. This process should be conducted carefully to avoid any damage to the part.
Step 7: Finishing Operations
Depending on the specifications, the part may require additional finishing operations such as trimming, painting, or assembly.
The Future of Precision Plastic Injection Molding
The future of precision plastic injection molding looks promising, with advancements in technology paving the way for even greater efficiency and sustainability:
- Automation and AI: The integration of artificial intelligence and robotics into the molding process will enhance precision and reduce operating costs.
- Bio-Based Plastics: The development of sustainable materials will allow manufacturers to produce eco-friendly products without compromising quality.
- 3D Printing Innovations: Combining 3D printing with injection molding will open new avenues in design and custom manufacturing.
Conclusion
In conclusion, precision plastic injection molding is a vital technology that is transforming the way industries manufacture their products. With its ability to create complex, high-quality components efficiently, it plays a significant role in various sectors, including automotive, medical, and consumer electronics. As technology advances, the benefits of precision plastic injection are expected to grow, making it an indispensable tool for innovative manufacturers worldwide.
For companies looking to enhance their manufacturing processes, exploring the potential of precision plastic injection molding could provide them with a competitive edge. At deepmould.net, we specialize in delivering high-quality injection-molded components tailored to your specific needs, ensuring your business stays ahead in an ever-evolving marketplace.