Ensuring Safety in Industries: The Indispensable Role of H2S Gas Detectors
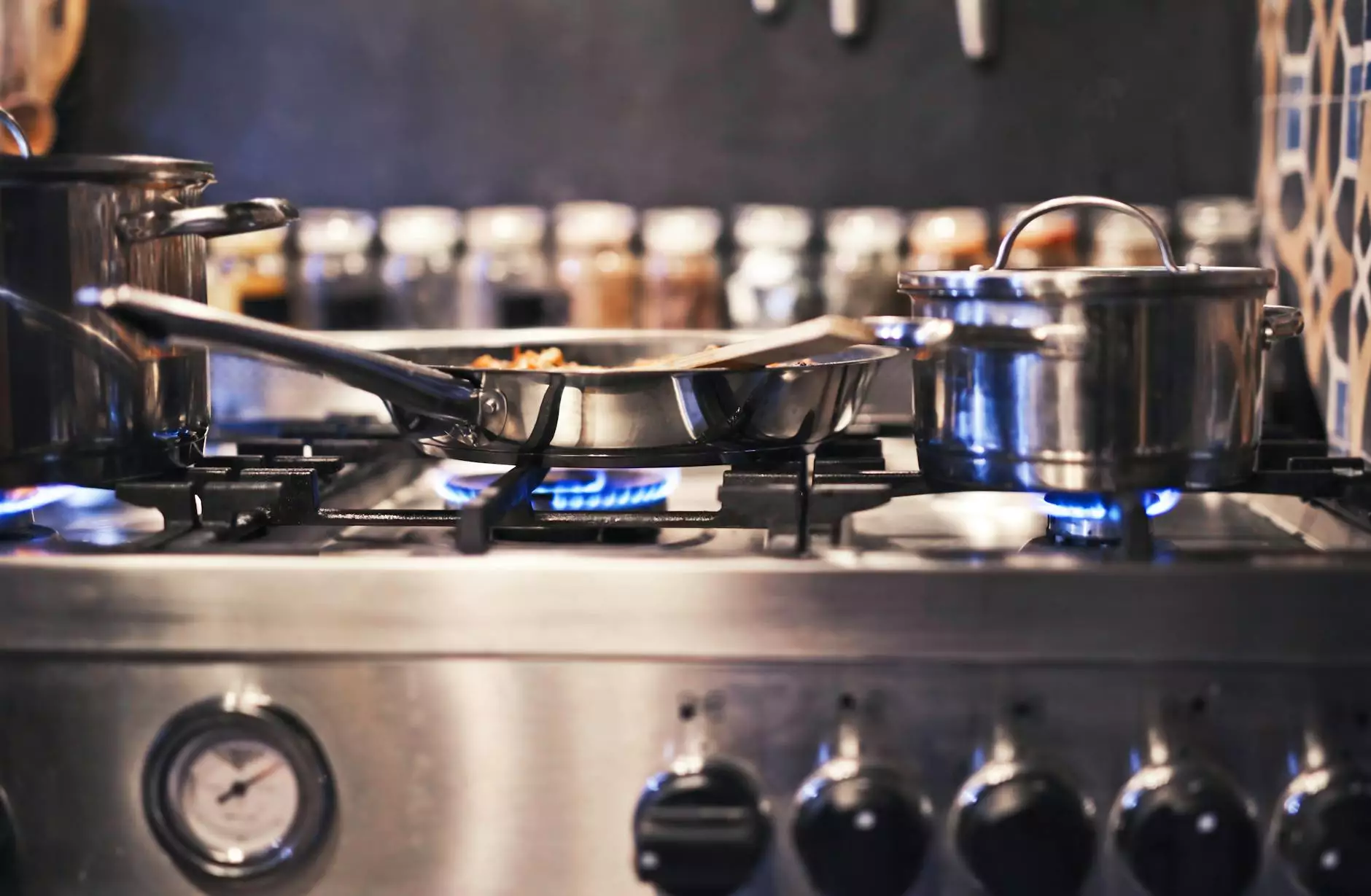
The presence of hazardous gases in industrial settings poses significant risks to worker safety. One of the most dangerous gases that can be encountered is hydrogen sulfide (H2S), a colorless gas with a distinct odor of rotten eggs. To mitigate the risks associated with this deadly gas, the use of an H2S gas detector is crucial. This article delves into the factors surrounding H2S gas, the functionality of gas detectors, and their importance in maintaining a safe working environment.
Understanding H2S: A Hazardous Gas
Hydrogen sulfide is a byproduct of various industrial processes, particularly in oil and gas industries, sewage treatment plants, and some manufacturing processes. Although it may be present in trace amounts, H2S can pose serious health risks and can be lethal in higher concentrations. Understanding these risks is essential for anyone working in environments where H2S may be present.
Health Effects of H2S Exposure
- Low Concentrations (0-10 ppm): May cause irritation of the eyes, nose, and throat.
- Moderate Concentrations (10-100 ppm): Can lead to dizziness, headaches, and nausea.
- High Concentrations (100-200 ppm): Causes severe respiratory distress and loss of consciousness.
- Very High Concentrations (above 200 ppm): Can be fatal within minutes due to respiratory failure.
The Role of H2S Gas Detectors
To ensure safety in environments where H2S is a concern, it is essential to have effective monitoring systems in place. This is where H2S gas detectors come into play. They are designed to constantly monitor the air for the presence of this hazardous gas and alert workers when levels become dangerously high.
Features of H2S Gas Detectors
Modern H2S gas detectors come equipped with several features that make them indispensable for industrial safety:
- Continuous Monitoring: These devices provide real-time monitoring of H2S levels, ensuring immediate detection of dangerous concentrations.
- Audio and Visual Alarms: When H2S levels exceed safe thresholds, detectors activate loud alarms and flashing lights to alert personnel.
- Portability: Many H2S detectors are portable, allowing workers to carry them into confined spaces where gas accumulation may occur.
- Data Logging: Advanced models can log data over time, providing valuable insights into gas presence patterns and potential leaks.
- Calibration Features: Many detectors come with built-in calibration options to ensure accuracy in measurements.
Types of H2S Gas Detectors
There are several types of H2S gas detectors available, each suited for different applications:
- Fixed Detectors: Installed in permanent locations, these are used for continuous monitoring in industrial facilities.
- Portable Detectors: Designed for field use, these handheld devices allow workers to monitor their surroundings as they move about.
- Personal Monitors: Worn on the body, these devices provide an added layer of safety for individual workers in high-risk areas.
The Importance of Training in H2S Detector Usage
Even with the best H2S gas detectors, the effectiveness of safety measures heavily depends on the training of personnel. Workers must be well-educated about H2S hazards, the functionalities of detectors, and proper response procedures in case of an alert.
Key Training Components
To optimize safety protocols, training programs should cover:
- Understanding H2S Risks: Workers should comprehend the properties and potential dangers of hydrogen sulfide.
- Proper Equipment Use: Comprehensive training on how to operate detectors accurately is crucial.
- Emergency Response Procedures: Knowing how to respond when a detector alarms can save lives.
- Regular Drills: Conducting regular safety drills helps reinforce training and ensures preparedness for real-life situations.
Regulatory Compliance and Best Practices
Compliance with safety regulations regarding hazardous gases is mandatory in many regions. Organizations must adhere to standards set by regulatory bodies such as OSHA (Occupational Safety and Health Administration) and NIOSH (National Institute for Occupational Safety and Health). Appropriate use and maintenance of H2S gas detectors play a critical role in achieving this compliance.
Best Practices for H2S Gas Detection
To enhance safety and ensure regulatory compliance, consider the following best practices:
- Regular Maintenance: Schedule routine inspections and maintenance of H2S detectors to ensure their operational effectiveness.
- Calibration: Calibrate the detectors according to the manufacturer's guidelines to maintain accuracy.
- Keep Records: Maintain logs of inspections, calibrations, and any incidents related to H2S exposure.
- Upgrade Equipment: Stay updated with the latest technology in gas detection to improve safety measures.
Conclusion: The Future of H2S Gas Safety
As industries continue to evolve, the importance of effective safety measures cannot be overstated. H2S gas detectors are a critical component in safeguarding workers against the dangers posed by hydrogen sulfide. Investing in quality detectors, providing ongoing training, and adhering to best practices will foster a culture of safety that not only protects workers but also enhances operational efficiency.
Ultimately, a proactive approach to managing hazardous gases leads to a more secure working environment, demonstrating an organization’s commitment to the well-being of its employees. At h2sonlinetraining.com, we emphasize the importance of education and training in ensuring effective use of H2S gas detectors. Let us work together to promote safety in all industrial settings, creating a safer tomorrow.